Companies grapple with post-pandemic inventories dilemma
Companies have to decide to maintain costly extra stockpiles or risk getting caught out again
Investing experts share their post-COVID portfolios
Oppenheimer managing director Jason Helfstein joins Commerce Street Capital CEO Dory Wiley on 'The Claman Countdown'
Companies are wrestling with how big their inventories should be, since the pandemic highlighted the dangers of having both too much and too little stored away.
When the pandemic first struck, and demand for many goods dived, some companies were left holding large, costly inventories. But closed borders, strained supply chains and rebounding demand meant bigger stock buffers can prove positive.
Now, the question of whether to maintain costly extra stockpiles or risk getting caught out again by disruption has emerged among the host of dilemmas businesses face, from whether to reshore production to how to best transport goods.
Companies on the S&P 500, excluding sectors that have few physical stockpiles like finance, increased their inventories by an average of 15% in the second quarter versus the comparable period in 2019, according to S&P Global Market Intelligence. Those inventories were 53% higher than the 10-year pre-Covid quarterly average.
Businesses from Nissan Motor Co. to PepsiCo Inc. say the decadeslong trend of hyper-efficient supply chains, often referred to as "just in time" manufacturing, could be ending. In a speech in October, President Biden said the world needed to take a longer-term view, as he announced measures to help alleviate port congestion.
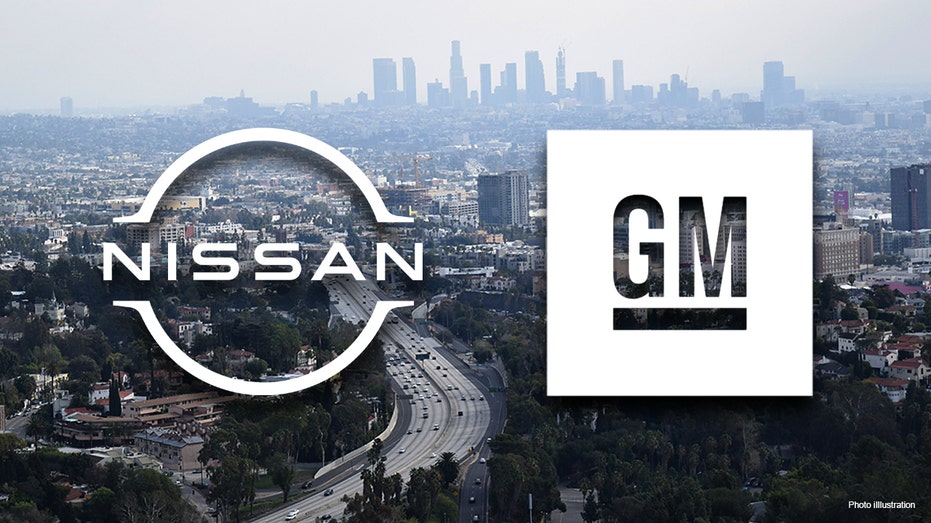
Photo credit: iStock
However, many companies say they will likely return inventories to pre-Covid levels when trading conditions normalize. Holding large inventories ties up capital, requires extra space and people to manage it and needs to be insured. It is also a problem for companies selling products with a sell-by date.
US COMPANIES BET SHOPPERS WILL KEEP PAYING HIGHER PRICES
Since the start of the pandemic, Austrian construction giant Strabag SE has squirreled away so much extra building material, like steel and lumber, that rivals sometimes accused it of buying up everything, said Thomas Birtel, its chief executive. But that move isn’t a lasting change in strategy.
"Our margins are so, so narrow that as soon as the situation and the ability to deliver has normalized, we will come back to a normal rhythm," said Mr. Birtel.
Kevin Keegan, an inventory-planning expert at consulting firm PricewaterhouseCoopers, said his clients tell him they will draw down inventories once supply chains recover. "Cost is still the driver for companies," he said.
Others worry that stockpiling products could leave them sitting on goods that expire.
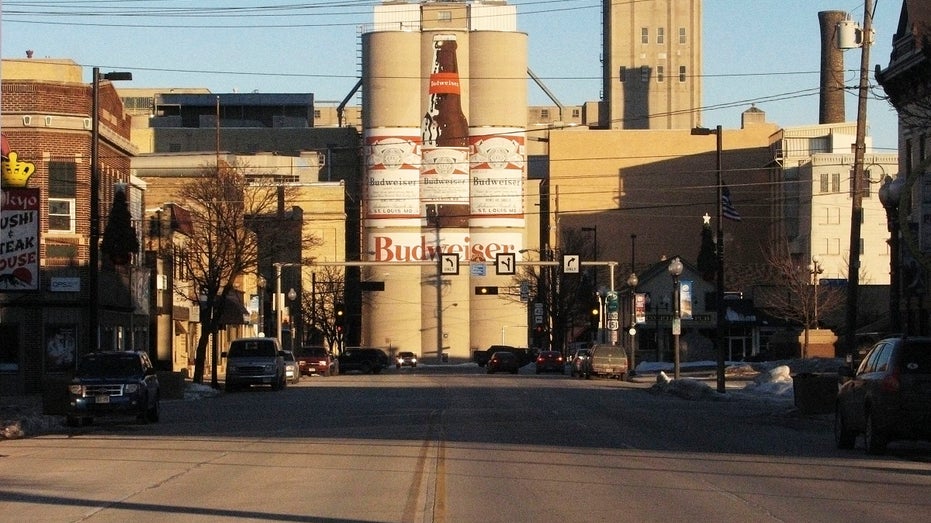
A mural of a Budweiser bottle and two Budweiser cans painted on a malt plant overlooks downtown Manitowoc, Wisconsin, January 18, 2016. The television documentary "Making a Murderer," -- from the case against Steven Avery and Brendan Dassey, who were
Incyte Corp.’s inventory of finished products was 156% higher in the second quarter than in the same period of 2019, partly because the drugmaker was seeking protection against supply-chain disruption. Finance chief Christiana Stamoulis said she expected inventories to return to pre-pandemic levels next year, once supply chain strains ease.
"We had an approach [pre-pandemic] that worked well," she said. "You don’t want inventory that would expire."
Inventories can be problematic going into a demand shock like a pandemic. Companies like car makers and luxury-goods brands were left sitting on stockpiles they couldn’t use when demand collapsed last year. Drinks companies including Guinness maker Diageo PLC and Budweiser brewer Anheuser-Busch InBev SA shared the cost of undrunk beer with their distributors to spare bars and restaurants from picking up the tab during lockdowns.
YELLEN SAYS AMERICANS HAVEN'T EXPERIENCED CURRENT INFLATION RATE 'IN A LONG TIME'
In the first four months of 2020, as the virus took hold, shares of S&P 500 companies that had higher inventory levels fell much further than those with slimmer stockpiles, according to a study by New Zealand’s Auckland University of Technology.
"The costs of carrying inventory during the period of depressed consumer demand and sales outweigh the benefits of inventory holdings as a buffer against supply-chain disruptions during this pandemic," the research paper concluded.
Still, some companies say their inventories will remain higher or be spread across locations. For years, German forestry-equipment seller BaSt-Ing GmbH used to order parts around a week before needing them, but the pandemic left the company struggling to secure what it needed. The firm has increased inventory of some parts to levels that will cover it for the next six months, up from the usual one- to two-month coverage.
"We always used to order just-in-time, now we had to shift to just-in-case," said managing director Josef Strobl, adding that he would wait to see how supply-issues shake out before deciding whether to resume his previous strategy.
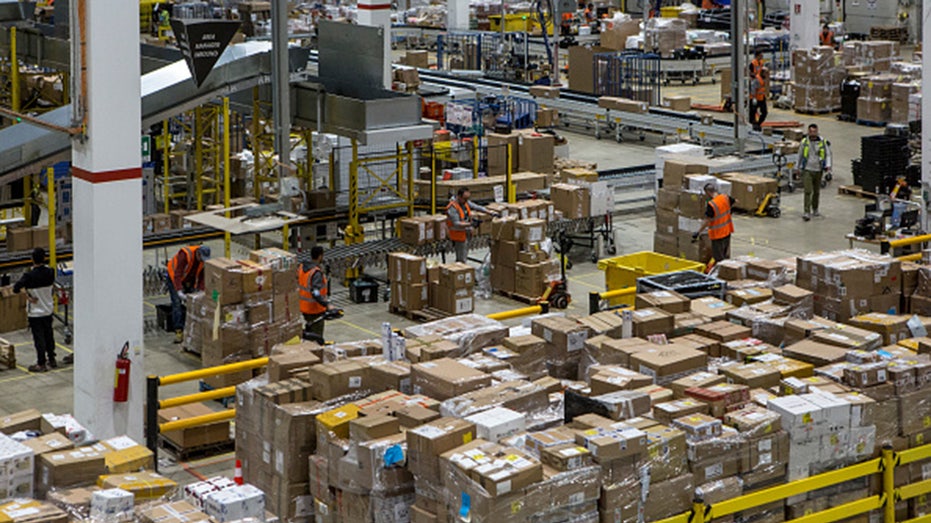
CASTEL SAN GIOVANNI, ITALY - NOVEMBER 17: A general view of the inbound area of the Amazon.com MPX5 fulfillment center on November 17, 2017 in Castel San Giovanni, Italy. Established in 2014, the 100.000 sq. metres warehouse employs a workforce of 1.
Gilead Sciences Inc. said it was significantly increasing its inventory of auxiliary products and tools, like syringes, glass vials and filters, which were suddenly in shortage during the pandemic.
"If you don’t have them, you can’t make the product," said Ken Kent, who manages manufacturing operations at the U.S.-based pharmaceutical company. Previously items like syringes were "kind of ubiquitous," he added.
"Accountants love [just in time], but the end, buyers don’t like it. I call it just-not-in-time," Mr. Kent said.
GET FOX BUSINESS ON THE GO BY CLICKING HERE
Other companies say they will likely go back to normalized inventory levels, but will change how they manage them. For instance, some multinationals—including Incyte—plan to decentralize stocks to place them closer to customers, giving them localized stockpiles to dip into during supply-chain strain.
Swiss drug giant Novartis AG is working to ensure each country it sells to has a second supply point for key products.
"One thing we learned last year was to have strategic inventory in more places...decreasing the dependency on single locations," said Amit Nastik, head of operations for Novartis’ manufacturing and supply organization.